Green steel in China: easier said than done
China steel is in its post-peak era – but can it get on an emissions pathway?
4 minute read
Isha Chaudhary
Global Head of Steel, Raw Materials and Alloys Markets

Isha Chaudhary
Global Head of Steel, Raw Materials and Alloys Markets
With 15 years of experience in metals and mining, Isha drives research and analytics for the ferrous space.
Latest articles by Isha
View Isha Chaudhary's full profileTi Guo
Managing Consultant, Iron Ore and Steel Cost Research
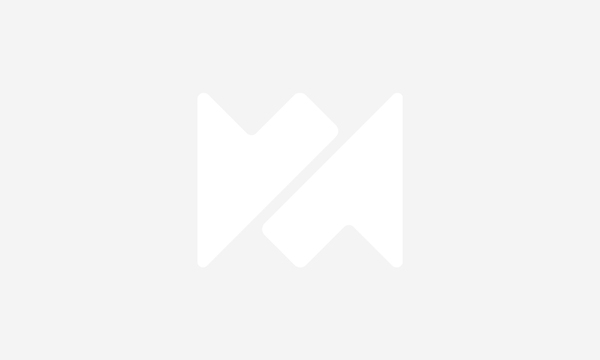
Ti Guo
Managing Consultant, Iron Ore and Steel Cost Research
Ti is focused on understanding iron ore and steel supply/demand dynamics and market trends in China.
View Ti Guo's full profileChina's steel sector was in the red for most of 2024. Patches of growing demand from energy transition and manufacturing have not been enough to cover up the property slack, and the billion-ton steel industry is edging toward another shake-up as barbed wires emerge across most trade borders. The current overcapacity of more than 50 Mt will balloon to 250 Mt over the next ten years.
Amid all this, the carbon problem seems to have been somewhat forgotten. And the problem is significant. China’s steel sector emits 2.2 gigatons of carbon, making it one of the most carbon-intensive industries.
The transition to green steel is particularly challenging due to the sector's giant, young and fragmented blast furnaces – with 200 firms, 360 mills and an average furnace age of just 12 years. Further, only 30-40% of steel production in China has green energy neighbours in proximity, making the transition complex.
The limited progress towards green steel production in China is evidenced by the scarcity of environmentally-focused initiatives. Of more than 250 green steel projects announced worldwide, a mere 15% are concentrated in China. Moreover, the majority have less ambitious carbon reduction potential than their global counterparts.
A new report, China steel in its post-peak era, draws on unique insight from our Steel Product Suite to explore the future of China's steel industry and the policy actions that will help it overcome the myriad of challenges.
Fill in the form to download a complimentary extract, or read on for an introduction to some of the key themes.
Trade barriers bring back steel’s overcapacity hangover; deja-vu 2015
After peaking at 110 Mt in 2024, China’s steel exports will take 6-8 quarters to normalise to the ‘business as usual’ levels of 75 Mt as an aftermath of multiple trade barriers. Weakening exports and frail domestic demand have created a near-term problem of 50 Mt of overcapacity. As steel demand contracts by 8% by 2035, redundant capacities will further balloon to 250 Mt.
The options to manage this overcapacity with limited social impact are limited:
- Encourage consolidation, as the share of the top 10 firms in China’s steel production is 44%, far from the consolidation target of 60% by 2025. The top 10 steel firms enjoy healthy utilisation of more than 95% while the remaining 190 firms operate at 65-70%, and could be potential consolidation targets
- Phase out high carbon-emitting mills
- Capacity swaps of blast furnaces with only electric arc furnaces (EAFs).
Meeting EAF targets needs a carbon price of US$60/t
Scrap EAFs will be China’s biggest answer to the carbon problem. Unfortunately, it has failed to take off in the last five years, being at a stalemate at 9-10% of production. Meeting its unofficial EAF production target of 15% by 2025 and 20% by 2030 now appears as a distant dream.
The tight scrap supply and the resultant high cost of EAF steel are the obvious antagonists for the slow take-off. At the current levels, a carbon price of US$60/t will help bridge the cost differential between EAF steel and basic oxygen furnace (BOF) steel in China. Some recent policies show promising progress. Integrating the steel sector into China’s carbon markets has been the first step. Setting up China Resources Recycling Group as a national platform for recycling and reusing resources is another good step in the right direction. Setting the stage before obsolete scrap hits the market will help speed up the process.
The hard choice to go green; hybrid solutions could help
Going green is a difficult path for a young and financially fragile sector, but a calibrated approach could help. China’s steel mills have room to optimise their blast furnaces, which can trim 20-25% of their emissions footprint.
To see how this might be achieved, fill in the form to download an extract from the full report.
Expensive opportunity to knock in 2030
Around three-fourths of blast furnace capacity in China will reach mid-life by 2030, and will require a relining overhaul capex to survive for the next 20+ years. Government and steelmakers are presented with a hard choice here: to reline the blast furnaces and lock in 34 GT of emissions for the next two decades or replace them with EAF and reduce emissions by two-thirds.
However, the decision is more complex than it appears due to the associated opportunity cost. When factoring in capital expenses, increased operational costs and carbon pricing, opting for the EAF route would result in an 8% higher cost – approximately US$625 per ton of crude steel (tcs) compared to US$575 per ton for the relined blast furnace method.
In other words, carbon prices would need to be twice our base case in China for economic parity between replacement and relining. In our base case we assume carbon cost will rise to US$70-80/t by 2050 and average at US$45/t during the 2030-2050 period.
Steel emissions reduction pathway beyond the base case needs active policy support
In our base case, China’s steel sector emissions reduce by 46% to 1.2 Gt by 2050. Not surprisingly, more than half of the reduction is being driven by a structural decline in steel production as China's economic growth becomes less steel-intensive. Optimisation will help the cause in the current decade, while scrap will take charge post-2035.
Our complimentary report extract includes a graphic highlighting the potential impact of hydrogen and carbon capture, utilisation and storage – and underlining the need for active policy support to support green steel projects in China. Fill in the form at the top of the page for your copy.